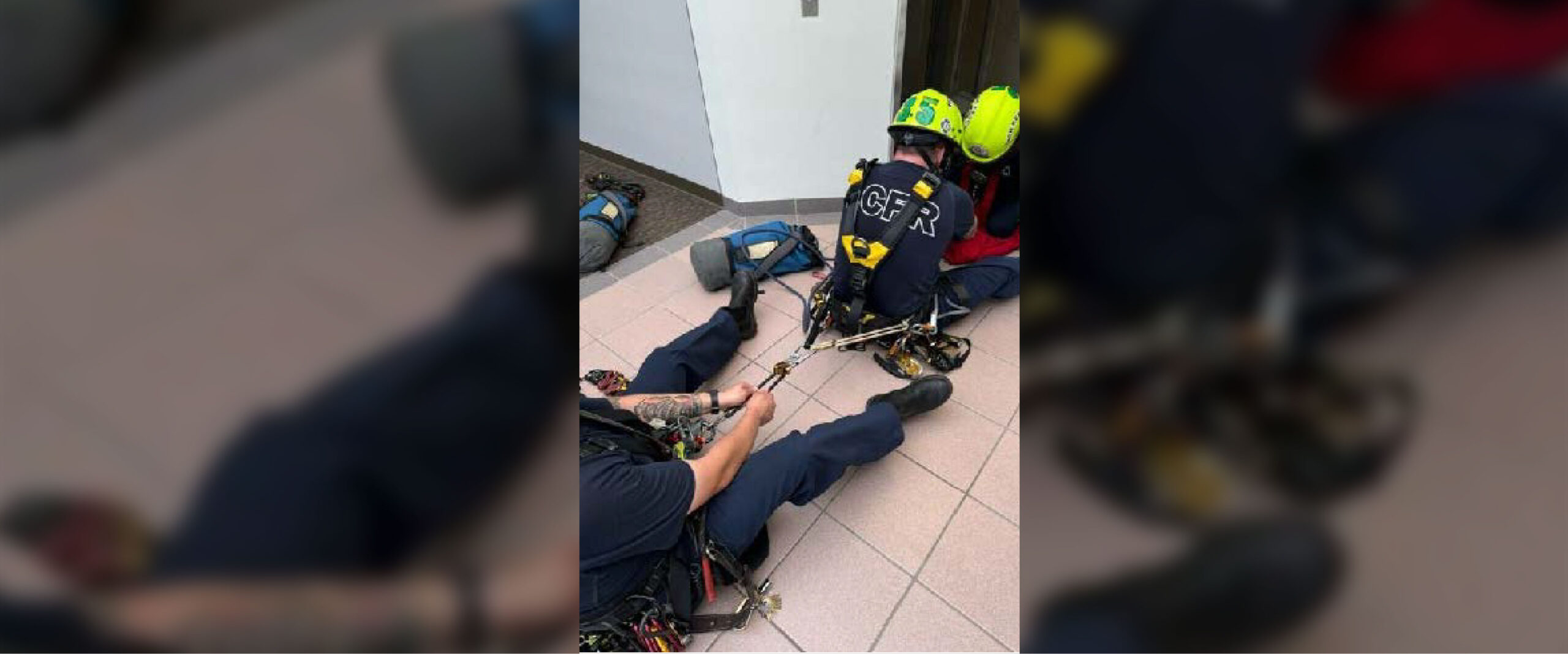
ITRS 2024 Presentation: Meat Anchors - Applying Force Measurement to Human Anchoring
Jason Ilowite, Lieutenant with Loudoun County (VA) Fire Rescue, and a CMC School Instructor, presented at the 2024 International Technical Rescue Symposium (ITRS) Conference in Golden, CO. His presentation titled “Meat Anchors: Applying Force Measurement to Human Anchoring,” was voted the “Best Overall” presentation from the ITRS audience.
In his presentation, Jason describes how test data is missing when determining whether the use of meat anchoring for rescue is safe and reliable. As stated in his paper, the term “Meat Anchors” refers to using a human as the anchor in a rope system, a practice widely utilized across various fields like recreational climbing, canyoneering, and firefighting for steep descents or rapid rescues. While its effectiveness is generally accepted, there is a lack of empirical data supporting its safety and reliability. Despite its documented usage, a review of existing resources revealed minimal research or force analysis related to meat anchors. To address this gap, testing and data collection are necessary to validate its application in rescue operations, moving beyond anecdotal evidence to informed, data-backed practices. Read his presentation below or on the ITRS website, alongside papers from other conference presenters.
About ITRS
CMC takes pride in co-founding and co-sponsoring the International Technical Rescue Symposium (ITRS), an annual gathering that brings together a diverse array of professionals in the technical rescue field. This includes experts in fire, mountain, cave, urban, industrial, and swift water rescue. At the symposium, presenters willingly share their research findings, testing outcomes, and field experiences for the collective benefit, encouraging attendees to reflect on and implement these insights. The symposium’s scale provides an ideal setting for extensive discussions and the exchange of knowledge.
Meat Anchors: Applying Force Measurement to Human Anchoring
By Jason Ilowite
Introduction
“Meat Anchors” refers to the practice of using a human to serve as the anchor for a rope system. This concept is not new by any means, and the tactic can be found in documentation spanning across several industries. Recreational climbers use this technique in their normal operations, canyoners use meat anchors to protect a steep down climb, and firefighters use the technique to conduct rapid rescues in hostile environments. Most people in any of these genres of rope work can all agree that meat anchors work and have a very valuable place in their respective activities. Like any good rescuer however, we should be seeking out empirical data to support our positions with any technique we choose to employ on the rescue ground. After searching far and wide, only one online blog post mentioned anything about force as it relates to meat anchoring. We decided to take a deep dive into force measurement on meat anchors in a quest to answer the question, “Does data from testing support the use of meat anchoring for rescue?”. Without numbers, anything we discuss with other rescuers really is only conjecture. Sure, we can say that we have used meat anchors in training, and possibly even real rescues, but without any sort of data to support our love of meat anchoring, we’re left stranded with a good idea.
Testing Process
In order to get the data we wanted, it was imperative to set up a testing method that was consistent, realistic, and easily repeatable. Keep in mind, our testing was as “back yard” as it gets. As much as most of us firefighters like to think we are a jack of all trades, we are certainly far from scientists. With that said, it is my belief that we came up with a testing method that met all our criteria. Testing was conducted primarily in two places. An abandoned building/parking garage, and a home made prop at our firehouse
The prop we built consisted of two Paratech struts spanning a second-floor doorway. We used 4×6 material to custom cut blocks to fit flush against the metal doorway set in a cinderblock wall. Paratech U-channels were than nailed to the blocks, and the struts placed in each u-channel respectively. The Paratech struts were pressurized into the door frame by utilizing a Paratech hammer to tighten the locking collar. The technical manual for the Paratech elevator rescue kit outlines a rating for grey struts to be loaded at their midpoint, making our operation compliant with manufacture’s guidance. We used two struts, stacked over top of each other with about 4’ of space between them. This simulated a “wall”. The rope would run over the top strut, and the meat anchor would use the bottom strut to brace their legs. The space the testing would be conducted in consisted of a smooth concrete floor. This was done intentionally in an effort to establish generalized “guard rails” for meat anchoring best practices; if what we tested would work on a floor with absolutely no surface friction, then it would work anywhere. We recognized that simply running rope over the smooth, cylindrical, metal surface of a strut would not mimic real world edge conditions. To remedy this, we constructed a box of sorts out of 2×6 material that would fit over the top strut and simulate a realistic 90-degree edge.
To make the tests relatively easy to reset, we utilized an AZTEK kit to hoist up a litter filled with gym plates. We obtained a static weight on this before testing to ensure it was exactly 2kN. One guiding principle for us was the desire to measure force on our meat anchors utilizing a 2kN load. We all know that a single person load is totally good to go, so much that the force is likely insignificant. But the question is, can meat anchoring be safe with a 2kN load, and if so, what conditions created the safety. All numbers were gathered simply by placing a CMC enforcer load cell between the descent control device and the meat anchor. Nothing extravagant, but highly effective.
Firefighter Escape and Civilian Rescue
The first set of tests revolved around the most likely scenarios that firefighters will encounter that would necessitate some sort of rope system. These types of incidents are never one that allows for time. It will always be a critical emergency, with time being the ultimate enemy. Many of these rescues have been highly publicized over the years. A very notable one was the famous Rescue on Broadway in 1991 where FDNY firefighters utilized meat anchors to lower a rescuer to pickoff civilians under fire conditions. The most common scenario that fire service personnel think of when they ponder the employment of a rope rescue on the fire ground, is a situation in which either a firefighter or civilian is trapped at an upper-story window, and rescuing them from the ground is either going to be so delayed rendering the option obsolete, or it is impossible all together. Situations like this can arise due to construction found all over the country. One notable instance was on January 23, 2005 in New York City during a fire in an apartment building with several illegal modifications made to it. A group of firefighters became trapped on the top floor. Several of them ultimately jumped killing two immediately and critically injuring four others. The access to the rear of this building was extremely difficult which significantly delayed the ability to get ladders etc. to the trapped firefighters. It seems as though many in the fire service directly correlate the use of meat anchors for roof-rope rescue evolutions with very large urban fire departments. Interestingly, suburban jurisdictions that are seeing rapid growth have the same potential for these problems traditionally associated with being an exclusively urban problem. Loudoun County, VA has been the fastest growing county in the nation for several years. The proximity to Washington, DC and other major infrastructure like Dulles International Airport has driven never ending construction for a couple decades. A common building layout we are seeing much more of, are either “U” or “Doughnut” shaped apartment buildings, with a completely enclosed courtyard. These buildings are lightweight, wood frame construction with a sprinkler suppression system. The suppression system would likely get overwhelmed and rendered useless in the event of a fire due to the fire load from modern construction materials. There is a huge life safety hazard with these buildings. If a civilian gets pushed out to their balcony facing the courtyard during a fire, any sort of ground ladder operation is going to be hopelessly delayed. There is no access from the outside of the building into the courtyard. It would require companies running large ground ladders through the building, and several fences to get to the courtyard. The answer is a roof-rope rescue operation, no different than what has been seen over the years in the nation’s largest urban departments.
Meat anchoring has seen a sharp increase in popularity on social media across the fire service. Many are starting to see the benefits of the technique, yet a large contingent of firefighters seem to still view meat anchors as a taboo, fringe, “cowboy” if you will method to conduct a rescue on the fire ground. A huge motivator for this ITRS presentation was to give fire service members everywhere the data necessary to develop confidence in using meat anchors when necessary. It is vitally important to note for those readers from other rescue genres who have nothing to do with firefighting; all the testing we did for fireground rescue scenarios can and should be applied to technical rope rescue as well. The only difference is we used firefighter escape kits for this section, the concepts would work exactly the same with rope rescue equipment.
We tested the following conditions to measure force on our meat anchor(s):
- 2kN load 1 meat anchor
- 2kN load 2 meat anchors with drop-loop 2:1
- 2kN load 2 meat anchors side-to-side with load sharing strap
- 2kN load 3 meat anchors in “flying V”
All tests were conducted two times each. Once the meat anchor would be “unsupported” and the second test they would be “supported”. The defining difference between the two would be the ability for the meat anchor to brace their legs on a wall in front of them vs not bracing on anything. While we all had strong suspicions that a non-supported meat anchor would perform poorly, we tested it as a potential variable to contend with in a real situation i.e a structurally unsound parapet wall.
A 2kN load with a single meat anchor and ropes running over a 90-degree edge, placed almost exactly 1kN on the meat anchor. We operated this system as a TTRS with two CMC LEVR escape kits. We found that with a 2kN load there is much more control over the descent with two escape kits rather than one, in addition to all the other reasons why we elect to use TTRS for rescue. This was the first lightbulb moment; edge friction is generally the enemy of a rescue system. It is clear that edge friction is the meat anchor’s best friend.
As our introduction to testing with more than one meat anchor, we wanted to know just how much more manageable the force would be if we added MA between the load and the meat anchors. Knowing that a 2kN load put a 1kN load on a single meat anchor, it seemed like an even cooler thought that we can divide that force in half again and split it between two people. This is exactly what happened, each meat anchor felt roughly 100lbf with a 2kN load by employing the “drop loop 2:1”. Disclaimer…obviously in a firefighting situation where we are using escape kits to do this method, it is most likely not going to get you to the ground. Most kits are roughly 50’ of rope or webbing. The thought here is that we can conduct our pickoff and then lower one or two floors below the fire to safety, and swing back into the building for removal of the victim.
Continuing with the idea that two meat anchors are better than one, we were looking for an effective way to have each meat anchor be an active participant. This was a relatively simple solution with the help of an Anderson Rescue Solutions Multi-Loop Rescue Strap. We use this strap heavily in our firefighting operations for drags etc, but the beauty of it is that it is also a rated anchor. We used the ARS strap as a two-point anchor between both meat anchors, with roughly a 30-degree interior angle (slightly wider). The descenders to control the lower were placed at the apex of the two point anchor and operated by one of the meat anchors. When the 2kN load was applied, the forces at each meat anchor did exactly what we would hope for with 30-degree-ish anchor angle. Each anchor was feeling about 150lbf, totally manageable.
The final test we ran involved the use of 3 meat anchors. Up to this point, the meat anchors slid when unsupported every single time, and a relatively low amount of force. Keep in mind, we were intentionally doing these tests on the building material equivalent of ice. The smooth concrete floor had absolutely zero surface friction, but this was intentional. We were on a quest to see if there was at least one way to not have the sliding if unsupported. The “flying V” meat anchor schematic was born (please see the Mighty Ducks movie for reference if needed). A second ARS strap was used to create an attachment to the rear of the lead meat anchor; something that a firefighter generally does not have. Meat anchors 2 and 3 sat side-to-side behind meat anchor 1, with the ARS strap being utilized as a two-point sling again. When the 2kN load was applied, some interesting things happened. This schematic was the only one in which no meat anchor slid on the smooth concrete. Meat anchor 1 lifted slightly off the ground but was easily held in place with 2 and 3 each seeing roughly 150lbf. It was our observation that when employing multiple meat anchors, it is better to spread them out in a wide footprint when possible. This is a big departure from the “backup” meat anchors just holding on through body contact as has been traditionally done in the fire service.
Technical Rope Rescue
As stated above, any of the techniques that were tested for firefighter escape/civilian rescue would work just the same in a technical rope rescue situation. In reality, the only thing that would separate the two is the gear used. On the fireground, personal escape kits will likely be used, whereas standard life safety rope, and descent control devices would be used for anything else. The necessitating circumstances to employ meat anchors remains the same; a victim is in critical need of immediate intervention, there are no suitable anchors that readily present themselves, and time doesn’t permit finding or building said anchors.
In addition to the initial testing we did with meat anchors, we endeavored to assess the feasibility of applying meat anchoring to technical rope rescues that often are very challenging to find anchors.
The “pass through” operation has become a go-to confined space entry technique for many reasons. The ability to anchor remote from the AHD allows systems to be operated away from the fall/atmospheric hazard that may be present by standing directly over the space in order to operate a block and tackle for instance. The pass through also allows the system to be rapid response. One side stays rigged for hauling, and the other for lowering, making any lapse time between the two operations virtually nonexistent. With all these benefits, the question becomes what to do when remote anchors don’t exist? Certainly, one could use their AHD as an anchor frame and run a traditional block and tackle or something similar. Meat anchors provide an immediate way to accomplish the pass-through rigging if your rescue takes you to an anchor wasteland. The roof of the pictured vacant building is exactly that. There are no adequate anchors anywhere close to where the operation needed to occur. Referencing above sections of this paper will show that the 2:1 drop loop placed the least amount of force on each meat anchor. The pass-through rigging includes a 2:1 pulley that the rescuer rides on. We were able to get the same benefit of the increased MA in addition to the differential nature of that pulley. Each meat anchor was feeling about 100lbf. This force dropped even lower on the haul side when raising.
Elevator hoistway rescues are relatively common across the country. On occasion, time to access the elevator car can become very crunched due to the condition of the patient. Being stuck in an elevator car for any length of time has the tendency to make many people claustrophobic, exacerbating any number of other conditions, and creating a real emergency. Unquestionably, an AHD is the best way to solve this problem, specifically the Appalachian Doortex using an Arizona Vortex. What is the answer however if a team doesn’t have a vortex? Or perhaps only certain units do, and their response is delayed? As in any other rope rescue, making access to the patient must be our number one priority. This sentiment generally results in teams without access to an AHD searching for alternative anchoring methods. It goes without saying that the inside of any office building wasn’t exactly built with rope rescue in mind. Many will result to anchoring on door hinges etc. Would you rather anchor to a door hinge, or a person? For these tests, we did not use a 2kN load, rather a 1kN load with the thought that this is an immediate access tool. Meat anchors likely won’t be what we will conduct the entire rescue on, but it is certainly how we would like to make access; and we’re never lowering more than 1 rescuer at a time in this application. In order to backup the lead meat anchor, a second meat anchor used the side work positioning rings of anchor 1’s harness to make a 2-point anchor with slings. A single attachment with a work positioning device is all that was needed to provide equal back tension on anchor 1’s harness. Anchor 1 had a very small amount of wall to brace their legs on resulting in anchor 2 not seeing any load. Anchor 1 felt around 170lbf on a TTRS. We also rigged the same scenario with the meat anchors sitting side-to-side with a load sharing strap between the two anchors. This placed the clutch in a much more favorable position for operation and was the preferred method.
In the second evolution, we placed a third meat anchor as a human high directional. To not have our human high directional exposed to a fall hazard by being right at the edge, we moved them back from the edge a bit. While moving them back did not provide as much help getting over the edge, it did do something, and it also resulted in less force being felt by that meat anchor to the tune of around 100lbf.
Meat Anchors and Safety Factors
Perhaps the most desired component of this entire paper/presentation is to provide enough data to persuade those who exclude meat anchoring from their rigging repertoire to change their outlook. Simply providing raw numbers is only part of that equation, the other component to a “warm and fuzzy” feeling is demonstrating that human anchoring does in fact include a safety factor. We recommend utilizing a TTRS system with your meat anchors whenever possible. Not only does this assist in having better control over a 2kN load, but we gain all the benefits already established by a TTRS.
As for quantifying an absolute safety factor when using meat anchors, the best we can reasonably do is account for a theoretical static system safety factor (SSSF). This is a ratio of the weakest link in the system divided by the weight of the load when everything is static. In the case of meat anchors, our testing has shown that a 2kN load placed 1kN on the meat anchor when running over a 90-degree edge. Assuming that there are two meat anchors either load sharing, or backing up, we are dealing with a 2kN anchor. This would give a theoretical SSSF of 2:1. While it doesn’t sound like a fantastic safety factor, it is certainly good enough for me in critical emergencies. It has been stated by some wise instructors in jest (kind of), that ultimately anything greater than a 1:1 safety factor is good enough to do a rescue. While we certainly always strive for better than that I do concur in certain situations.
Dynamic system safety factor (DSSF) is much more difficult to figure out. This is a ratio of the weakest link divided by the weight of the load during a dynamic failure event and requires that we have a good idea of what the max arresting force will be. Testing has shown that when using a TTRS, a failure of one half of the system can result in up to a doubling of the force on the surviving components. If we use the numbers for our SSSF, the 1kN on our meat anchors would turn into 2kN on a 2kN anchor; not good. The huge issue with figuring this out is, how do we know what amount of force a meat anchor can withstand? Is anyone willing to test dynamic failure events of a 2kN load when our anchor is a human? For this testing I certainly was not. This leaves us with a big unknown regarding reliably figuring out a dynamic system safety factor. We can reasonably assume that two meat anchors who are properly braced against an object and are sharing the load could likely withstand a lot more force than we give them credit for. This would shoot the safety factor numbers way up; but once again, how do we safely test for that number? If any of the readers out in the world have a good solution for this, I would love to know about it!
An additional complicating factor for analyzing a real safety factor number, is the weight of the meat anchor matters. We used industry standard numbers for our testing. 1kN for a single person, 2kN for two people. When analyzing rope rescue systems, these numbers generally get us “close enough”. We are using gear that is so strong, and unquestionably sound anchors, that the difference in actual weight is splitting hairs. When the anchors are humans, we know that the 1kN number assigned to a single person isn’t accurate. We have all seen a single person load that is over 1kN, just as there are plenty of single person loads that are well under 1kN. These numbers matter more than ever when trying to assign a safety factor to meat anchoring. There is so much variance that is makes the task virtually impossible.
Best Practices
A guiding principle of this presentation was to provide the reader with meat anchoring best practices that can be supported by data and easily implemented; they are below:
- Meat anchoring shouldn’t be “plan A”, but they also should not be hesitated upon. That is to say, it would not be good rigging practice to use meat anchors next to an unquestionably sound steel column that happens to be within the fall line. However, if you find yourself in a high-stakes emergency where time is of the upmost importance, and anchors are not readily available, rescuer’s should not think twice about using meat anchors, provided the rest of these best practices are adhered to.
- When using meat anchors, the load should be limited to 1kN as much as possible. Our testing has shown the effects of a 2kN load to demonstrate how meat anchors would perform in the event you must have a two-person load. Just because you can, doesn’t mean you should. If the load can be reasonably limited to 1kN, do so.
- Should you need to use meat anchors for a 2kN load, the rope must run over an edge (protected of course), and/or be backed up with other meat anchors. Ideally both of these conditions will be present. It is the most counter intuitive thought to intentionally use edge friction. Everything we know about rope rescue tells us to combat edge friction whenever possible. We have identified the caveat with meat anchors. Edge friction truly is the meat anchor’s best friend.
- Meat anchors should find bracing for their legs whenever possible. If none exists and you must use meat anchors, several should be utilized.
- If using multiple meat anchors, our testing demonstrated that they are best served in a way that increases the overall footprint of the meat anchor and distributes the load. Literally stacking other people on top of the meat anchor might be effective in some circumstances, but it’s not the best. By allowing additional meat anchors to use their full weight sitting next to, or behind the primary meat anchor, the overall anchor system is much more stable and effective. The side-to-side method, or the “flying V” are good options for this.
- Whenever possible, utilize a TTRS for any meat anchor operation. The rescuers will gain all the benefits that have been established with a TTRS, while also having much more control over heavier loads, and providing some redundancy.
Conclusion
Like most anything, this topic warrants much more testing and exploring of ideas. While we certainly did not answer every question with this testing (we might have actually created more), the hope is that we at least provided numbers for meat anchoring so the end user can employ the technique with more knowledge of where forces are being applied and how. The desired result of the knowledge gained is to give decision makers the faith in human anchoring if they ever find themselves in a predicament to use meat anchors.
A huge thank you is owed to Loudoun County Fire Rescue, and the members of Rescue Company 35 B-shift. Without their genuine desire to get to the bottom of new ideas and techniques, none of this would have been possible.